Hapa tunadili na mambo ya computer HARDWARE,SOFTWARE & NETWORKING.,desktop,laptop,notebook,pumtop,min.Pia tunauza desktop,laptop,tv,radio kwa bei nafuu,. KARIBU 0785345337 0653783670 0758088147
Thursday, December 13, 2012
UNATAKA KUJUA HABARI MPYA BOFYA HAPA
Haya habari nzuri kwa wazi wa dar-es-salaam kuanzi sasa niko free napatikana muda wote kama unatatizo na computer yako ya aina yoyote unaweza kunipigia kwa no hii 0689362431 muda wowote free call kubeep hairuhuciwi Karibun
Saturday, November 10, 2012
Troubleshooting the APC UPS and other UPS's
Troubleshooting the APC UPS and other UPS's
APC Smart UPS troubleshooting, battery problems, bug fixes and troubleshooting for most UPS systems.
APC Smart UPS Voltage Gain Bug: [Jump to it]
If you have a older APC Smart UPS and are having many strange problems with batteries, freeze ups, etc. chances are it's because of a bug that I have identified and confirmed in most older APC Smart UPS systems. There is a easy fix but please read this document in full to understand it.
APC UPS units are well built power inversion systems. However, problems do arise and in most cases it's not the direct fault of the UPS system but instead the consumable batteries.
This problem and technique applies to all UPS systems, regardless of make.
Top APC (and non-APC) UPS Symptoms:
Most lead acid batteries ship semi-charged, the charge level varies between them.
Most of the larger APC (and non-APC) UPS systems use higher voltages to reduce the size and weight of the transformer (thinner windings), reduce the size of DC battery cables and reduce the circuit board trace sizes (higher voltage means lower current). Common voltages include 24V, 48V and on some UPS systems even 120 VDC and above. The small UPS systems use a 12V (single) battery and rarely have the above problems, here is why:
While the larger voltage UPS's use higher voltages of 24 VDC and above, the batteries are still 12 VDC. So, to accomplish the voltage required the batteries are wired in a series configuration such as: - [-12v+]-[-12v+] + 24
We will use for example the APC Smart UPS 1400:
- Battery Voltage of 24VDC
- Unit uses (4) 12V batteries in (2) banks of 12 Volts, each of the 2 banks are in parallel, together both banks give 24 VDC.
- System by default maintains a charge/float voltage of 27.60 VDC, divide that by 2 and you get 13.80 VDC per 12VDC battery. Within range on most sealed lead acid batteries. (13.80/6 = 2.3 VDC per cell)
- As the battery pack (4 batteries) ages, some of the batteries may wear more then others which bring the serial configuration out of sync. In other words, 1 of the 4 batteries may actually have less voltage. So what happens is the voltage the unit is looking for cannot be maintained and the UPS system continues to charge even though the other batteries may be fully charged.
Now as a battery reaches full charge its current draw drops off and because the batteries are in series the other battery with a lower voltage in the serial array never can reach it's full charge. The UPS system senses the final voltage is reduced and when it cannot bring it up to the specified voltage, the unit triggers either a "Bad Battery" alarm or the unit shuts itself down to prevent damage.
The "Bad Battery" condition is triggered when:
Many times people will install new batteries and it will work but sometimes it still triggers a "Bad Battery" alarm and they fault the UPS System. However, when you order new batteries nothing says that the voltage of all of them will be the same and so when you connect them you will still be out of range or not synchronized.
Equalization Technique:
Read this very carefully a few times to make sure you fully understand this. Failure to do so could destroy your UPS system and/or batteries.
If using a 48VDC unit or above, the reading are different but still apply a 15VDC equalization charge with all batteries in parallel. Remember, make sure the batteries are in parallel to do the manual charge and equalization, not series!
In short, battery banks go out of "sync" and need to be equalized, even if they're brand new. Manufacturing processes often cause small voltage fluctuations between batteries and the UPS systems do not like this.
In some cases, the Smart UPS systems have trouble even after the above steps. From thorough testing and experimenting I have found that older model APC Smart UPS systems are operating at too high of a battery voltage gain causing all types of problems. The good news is that the APC Smart UPS charge controller is powered by a on-board microcontroller, and thus we will change it so that it's running at the correct setting, a big bug APC apparently fixed with newer revisions.
APC Smart UPS Battery Voltage Gain Bug and Fix:
Older model APC Smart UPS have a bug in the voltage gain, it's flat out wrong. It cooks batteries, causes premature battery failures, and all sorts of other problems including the system freezing up and shutting down AC power to the load. Even serial communications is lost in some instances requiring complete AC and DC disconnection. Almost all of these issues are in older Smart UPS systems running at around 2.3 VDC per cell voltages. Follow these instructions to reprogram the system voltage gain and solve your problems.
The following only applies to the APC SmartUPS. The below instructions are for the APC SmartUPS 1400 or any SmartUPS with a battery voltage of 24VDC. On 48VDC units, use 54.24 instead of 27.20. (or 2.26 VDC per cell)
By following the above instructions your unit will try to maintain a battery voltage of 13.56 volts (per battery) which eliminates many false alarms and will also greatly increase battery life and solve almost all of your problems. Combined with the equalization technique your system will last reliably for many years on new batteries. After the above change your unit is basically brought up to the newer revision. The voltage gain fix is the most major difference. 13.56 VDC is the lower range float voltage for most SLA (Sealed Lead Acid) batteries and also in range for flooded-cell lead acid batteries. Running each battery at 13.56 VDC (2.26 VDC per cell, or 27.20 in series) will significantly extend the life of the batteries but when using this voltage it is recommended to apply a 15VDC equalization charge every 6 months to maintain very long life. In many cases, UPS battery life's of up to 5 years!
There is actually a whole science behind float voltages and my highly tested advice does vary but in this case, 2.26 VDC per cell is best because of reduced charging temperatures, reduced battery gassing/electrolyte evaporation and better charging across a wide variety of temperatures. For extended battery life and reliability, there is a very slight decrease in battery capacity but is unnoticeable. I could get in to a whole other discussion on the physics behind lead acid batteries but please just take my advice, and you will be very satisfied with the outcome.
I also chose this voltage also because it allows us to use both SLA and regular car batteries (flooded cell) together, something the APC was not designed for but can now handle with this fix.
Although unconfirmed, it is my belief that APC was aware of this voltage gain problem and is why they were exchanging units with newer revisions. It would also explain why some APC Smart UPS use 27.67 VDC and others use 27.30 VDC voltage gains. Now that your unit is out of warranty, it's the only option to fix your unit.
The above information should fix about 95%+ of APC related issues. The equalization technique works with ALL UPS systems using multiple batteries in serial, basically any voltage 24VDC or above.
I have seen the strangest problems in UPS systems of all different manufacturers, it turns out almost always relating to the batteries being out of sync and/or the voltage gain bug. This is information you cannot find anywhere as APC and other sources just tell you to replace the battery and if it fails still replace the unit, not always our favored choice. You should change the voltage gain too even if the equalization technique solved your problems because it will also prevent future problems.
Get tremendous run time from your APC Smart UPS XL System using 2 or more automotive batteries
NOTE on wire: Make sure you use 6 gauge wire or heavier for the SU1400XL. #8 gauge is adequate but the SB connector for the external pack is only available for 6, 4 or 2 gauge wire. The SU1400 unit uses #10 gauge wire internally but it's a very short distance and the insulation is probably rated to a higher temperature. A typical way of cutting the cost of expensive copper wire.
APC Smart UPS troubleshooting, battery problems, bug fixes and troubleshooting for most UPS systems.
APC Smart UPS Voltage Gain Bug: [Jump to it]
If you have a older APC Smart UPS and are having many strange problems with batteries, freeze ups, etc. chances are it's because of a bug that I have identified and confirmed in most older APC Smart UPS systems. There is a easy fix but please read this document in full to understand it.
APC UPS units are well built power inversion systems. However, problems do arise and in most cases it's not the direct fault of the UPS system but instead the consumable batteries.
This problem and technique applies to all UPS systems, regardless of make.
Top APC (and non-APC) UPS Symptoms:
- Cooling Fan (if present) turns on and off constantly or does not shut off
- Loud continuous beep from UPS system
- Battery light comes on
- UPS System shuts down with no LED's, no response and a continuous beep (common to the Smart UPS)
- Internal relays "click" on and off repeatedly (common to the APC BG1500 Pro)
- Serial communication and/or SNMP Card "freeze" and communication is lost
- Unit must be unplugged and battery disconnected to reset
Most lead acid batteries ship semi-charged, the charge level varies between them.
Most of the larger APC (and non-APC) UPS systems use higher voltages to reduce the size and weight of the transformer (thinner windings), reduce the size of DC battery cables and reduce the circuit board trace sizes (higher voltage means lower current). Common voltages include 24V, 48V and on some UPS systems even 120 VDC and above. The small UPS systems use a 12V (single) battery and rarely have the above problems, here is why:
While the larger voltage UPS's use higher voltages of 24 VDC and above, the batteries are still 12 VDC. So, to accomplish the voltage required the batteries are wired in a series configuration such as: - [-12v+]-[-12v+] + 24
We will use for example the APC Smart UPS 1400:
- Battery Voltage of 24VDC
- Unit uses (4) 12V batteries in (2) banks of 12 Volts, each of the 2 banks are in parallel, together both banks give 24 VDC.
- System by default maintains a charge/float voltage of 27.60 VDC, divide that by 2 and you get 13.80 VDC per 12VDC battery. Within range on most sealed lead acid batteries. (13.80/6 = 2.3 VDC per cell)
- As the battery pack (4 batteries) ages, some of the batteries may wear more then others which bring the serial configuration out of sync. In other words, 1 of the 4 batteries may actually have less voltage. So what happens is the voltage the unit is looking for cannot be maintained and the UPS system continues to charge even though the other batteries may be fully charged.
Now as a battery reaches full charge its current draw drops off and because the batteries are in series the other battery with a lower voltage in the serial array never can reach it's full charge. The UPS system senses the final voltage is reduced and when it cannot bring it up to the specified voltage, the unit triggers either a "Bad Battery" alarm or the unit shuts itself down to prevent damage.
The "Bad Battery" condition is triggered when:
- [Most common] The battery pack stops drawing current before the "full" voltage threshold is reached. This will happen when a battery legitimately goes bad and it will no longer take a charge because of plate sulfation, loss of electrolyte or plate damage. But in other cases and even for new batteries this alarm can be triggered because one battery becomes full in the serial chain preventing the others from charging and the final battery pack output voltage is lower then the "full" voltage threshold. This is known as current controlled charging. Remember, as a battery charges it's current flow is reduced. When current tapers off but the voltage is still too low a "Bad Battery" alarm is triggered. Some older APC Smart UPS systems have a bug in the voltage gain parameter sometimes causing "Bad Battery" conditions to be triggered falsly because the voltage gain parameter is set too high. Luckily, there is a fairly simple fix.
- The battery continues to draw the same amount of current and the voltage does not change within a preset time.
- Too much current draw indicating a internal battery short or wiring short.
- Battery temperature (for units equipped with a sensor) is too high. Often a bad battery or internal battery short.
Sometimes the thermistor will also go bad and report incorrect temperatures.
Many times people will install new batteries and it will work but sometimes it still triggers a "Bad Battery" alarm and they fault the UPS System. However, when you order new batteries nothing says that the voltage of all of them will be the same and so when you connect them you will still be out of range or not synchronized.
Equalization Technique:
Read this very carefully a few times to make sure you fully understand this. Failure to do so could destroy your UPS system and/or batteries.
- Get new batteries (or try it with your current batteries)
- Wire all of the batteries in parallel together (+ goes to +, - goes to -)
- Use a volt meter to confirm your batteries are in parallel, if right you should read around 12 VDC (if charged)
- If your batteries are not charged, charge them in the parallel configuration above using a regular battery charger
- Now, we have to apply a equalization charge of 15VDC. Look for a wall transformer (or other source) that outputs 15VDC, if using just the internal battery pack look for one with at least 250mA output.
- Connect the 15VDC source to the parallel wired bank and let it sit for 2-4 hours
- After this is done disconnect the 15 VDC source, wire the batteries back in to the normal serial configuration, test the output is around 26-27VDC and connect it to the UPS system.
- Your problems should now be gone!
If using a 48VDC unit or above, the reading are different but still apply a 15VDC equalization charge with all batteries in parallel. Remember, make sure the batteries are in parallel to do the manual charge and equalization, not series!
In short, battery banks go out of "sync" and need to be equalized, even if they're brand new. Manufacturing processes often cause small voltage fluctuations between batteries and the UPS systems do not like this.
In some cases, the Smart UPS systems have trouble even after the above steps. From thorough testing and experimenting I have found that older model APC Smart UPS systems are operating at too high of a battery voltage gain causing all types of problems. The good news is that the APC Smart UPS charge controller is powered by a on-board microcontroller, and thus we will change it so that it's running at the correct setting, a big bug APC apparently fixed with newer revisions.
APC Smart UPS Battery Voltage Gain Bug and Fix:
Older model APC Smart UPS have a bug in the voltage gain, it's flat out wrong. It cooks batteries, causes premature battery failures, and all sorts of other problems including the system freezing up and shutting down AC power to the load. Even serial communications is lost in some instances requiring complete AC and DC disconnection. Almost all of these issues are in older Smart UPS systems running at around 2.3 VDC per cell voltages. Follow these instructions to reprogram the system voltage gain and solve your problems.
The following only applies to the APC SmartUPS. The below instructions are for the APC SmartUPS 1400 or any SmartUPS with a battery voltage of 24VDC. On 48VDC units, use 54.24 instead of 27.20. (or 2.26 VDC per cell)
- Connect your serial (APC) cable to the UPS and your computer
- Make sure the APC monitor service if installed is stopped otherwise the serial port will be in use.
- Open hyperterminal (On Windows start->run hypertrm)
- Create a new connection on the proper com port and use 2400 baud, 8-N-1 Xon/Xoff)
- Press Shift+Y you will get SM
- press 1 - wait a second - press 1 again
- you should see PROG
- type B
- A value of 27.XX should be read back. On older Smart UPS systems with the mentioned bug you will see 27.60, 27.67 or in some cases even higher. Newer revisions use 27.30, but even that is not our perfect setting and can cause issues. We're going to reprogram the system's EEPROM all together for the perfect setting.
- Press the - key (minus) then press B
- Repeat this step above until you see 27.20 (If you're on a 48VDC unit select 54.24)
- Confirm the setting of 27.20 by pressing B again
- Press Shift+R to exit
- Close hyperterminal
- Reset your unit (Disconnect battery and AC)
- You're done! If you didn't equalize your batteries, do it and the unit will function even better.
By following the above instructions your unit will try to maintain a battery voltage of 13.56 volts (per battery) which eliminates many false alarms and will also greatly increase battery life and solve almost all of your problems. Combined with the equalization technique your system will last reliably for many years on new batteries. After the above change your unit is basically brought up to the newer revision. The voltage gain fix is the most major difference. 13.56 VDC is the lower range float voltage for most SLA (Sealed Lead Acid) batteries and also in range for flooded-cell lead acid batteries. Running each battery at 13.56 VDC (2.26 VDC per cell, or 27.20 in series) will significantly extend the life of the batteries but when using this voltage it is recommended to apply a 15VDC equalization charge every 6 months to maintain very long life. In many cases, UPS battery life's of up to 5 years!
There is actually a whole science behind float voltages and my highly tested advice does vary but in this case, 2.26 VDC per cell is best because of reduced charging temperatures, reduced battery gassing/electrolyte evaporation and better charging across a wide variety of temperatures. For extended battery life and reliability, there is a very slight decrease in battery capacity but is unnoticeable. I could get in to a whole other discussion on the physics behind lead acid batteries but please just take my advice, and you will be very satisfied with the outcome.
I also chose this voltage also because it allows us to use both SLA and regular car batteries (flooded cell) together, something the APC was not designed for but can now handle with this fix.
Although unconfirmed, it is my belief that APC was aware of this voltage gain problem and is why they were exchanging units with newer revisions. It would also explain why some APC Smart UPS use 27.67 VDC and others use 27.30 VDC voltage gains. Now that your unit is out of warranty, it's the only option to fix your unit.
The above information should fix about 95%+ of APC related issues. The equalization technique works with ALL UPS systems using multiple batteries in serial, basically any voltage 24VDC or above.
I have seen the strangest problems in UPS systems of all different manufacturers, it turns out almost always relating to the batteries being out of sync and/or the voltage gain bug. This is information you cannot find anywhere as APC and other sources just tell you to replace the battery and if it fails still replace the unit, not always our favored choice. You should change the voltage gain too even if the equalization technique solved your problems because it will also prevent future problems.
Get tremendous run time from your APC Smart UPS XL System using 2 or more automotive batteries
- Apply the Voltage Gain Fix above (factory voltage too high for these batteries)
- Purchase 2 12V car batteries (Walmart has them from $55/each)
- Purchase 2 battery cables with battery post connectors (Walmart $5/each)
- Purchase 2 battery post connectors (Walmart $1.54/each)
- Purchase the external battery pack connector (Made by Anderson Power Products) available from powerwerx ($6). Make sure you match the SB connector to the external SB connector on the UPS. On a SU1400 it's the SB120 plug. [Buy from PowerWerx]. Also purchase a connector with the same gauge as the battery cable.
- Put the batteries side-by-side and connect + to - using the battery post connectors and some heavy gauge wire (#8/#6 or #4), then chop off the end of the battery cable (not the battery post, the other end), put it in the SB plug, crimp (or hammer the front nearest the wire). Do this for both the +/-, note the polarity on the plug and match to the right terminal. Should look like this - To UPS [Bat A] + to - [Bat B] + to UPS
- Make sure your voltmeter reads around 25 VDC.
- Temporarily take out of series, put in parallel, apply the 15 VDC equalization charge for 4 hours.
- Put back in to series, confirm you have 25 VDC, connect to UPS.
- You now have a UPS system that has a very long run time. About 150-200Ah compared to the 32Ah internal battery pack. You could add about another 1 (or 2) of these banks, I would not push it. On the 2nd or 3rd bank make sure you parallel these banks and don't put them all in series or you will blow your UPS through the roof. It's also recommended you connect a DC breaker or a fuse for protection against shorts. On the SU1400XL the proper fuse/breaker size would be 60 Amps.
NOTE on wire: Make sure you use 6 gauge wire or heavier for the SU1400XL. #8 gauge is adequate but the SB connector for the external pack is only available for 6, 4 or 2 gauge wire. The SU1400 unit uses #10 gauge wire internally but it's a very short distance and the insulation is probably rated to a higher temperature. A typical way of cutting the cost of expensive copper wire.
Sunday, November 4, 2012
how to repair video camera
ideo cameras, once a luxury, are relatively commonplace--especially
at youth sporting events. Your authors have countless hours of
long-forgotten high school baseball, football, track, cross-country,
swimming, and other events packed away somewhere. We've had a few
problems with video cameras over the years, so we know how to do some
basic repairs--and how to maintain them to avoid having to fix them.
How Does It Work?
A video camera, also called a camcorder, is a portable television
camera combined with a video recorder. The camera section has a lens and
special charge-coupled device or CCD (a microchip with thousands of
tiny light-sensitive elements containing photodiodes). The CCD separates
the picture into three color images using red, green, and blue color
filters over adjacent light-sensitive elements. In the recorder section,
the video signal from the CCD and sound signal from the video camera's
microphone are recorded on tape in the same way that a video recorder
records sound. The signal is either analog (older) or digital (newer).
The tape format may be VHS, VHS-C or 8 millimeter, but otherwise video
cameras are very similar in function, maintenance, and repair.
How Does It Work?
![]()
Components of a typical video camera.
|
Fix-It Tip
Some so-called problems are caused by built-in safety devices. For example, many video cameras will refuse to work if an internal sensor says that the air is too moist or dusty. In fact, a warning image may show up on the viewfinder or screen. If so, change conditions (if possible) before attempting to video. Canned air can assist the process.
Sunday, October 21, 2012
Replace Your Motherboard
Replace Your Motherboard
Learn how to transplant your PC's most important component.
By John Mwingira
If you are looking to use an updated processor, want to add some newer components that require the latest technology, or have shorted out your motherboard with an incorrect audio cable (not that we're speaking from experience), changing your motherboard is the way to go. Though the process looks daunting, it requires little more than a Phillips screwdriver and some patience. Here's everything you need to know.
If you are looking to use an updated processor, want to add some newer components that require the latest technology, or have shorted out your motherboard with an incorrect audio cable (not that we're speaking from experience), changing your motherboard is the way to go. Though the process looks daunting, it requires little more than a Phillips screwdriver and some patience. Here's everything you need to know.
Step 1: Assess the situation
Before you pull out your toolkit (or even your credit card), do a bit
of reconnaissance inside your PC. Some things to keep in mind:
If your case is a proprietary one from a major vendor, it might not easily house a replacement board. And if it's a small-form-factor PC, you won't be able to put a larger ATX motherboard into it. Make sure your case supports the form factor (ATX, MicroATX, and so on) of your new board.
Many older motherboards require a 20-pin main power cable from your power supply, but recent boards require both a 24-pin connector and a separate 4-pin one. Your motherboard won't work if improperly powered, so a new power supply could be in order.
Do your optical and hard drives connect via IDE (usually with ribbon cables) or via newer Serial ATA (thinner cables)? Many newer motherboards have only one IDE port (which supports two drives), whereas older boards have two. If you have more than two IDE drives, be sure your new board has a second IDE connector.
What kind of processor, RAM, and graphics card will you be using? What was top-of-the-line a few years ago could be obsolete today. AGP graphics cards certainly are—most newer motherboards lack slots for them, replacing them with PCI Express (PCIe). Processor socket technology and RAM design have also changed. If you don't want to buy all new components, make sure yours work with the new motherboard. Not sure what you have? A free utility like CPU-Z can suss it out.
Be mindful of Windows' licensing requirements—replacing a motherboard can necessitate reactivating Windows. Depending on whether you have a full-retail or OEM version, you may have to repurchase Windows.
If your case is a proprietary one from a major vendor, it might not easily house a replacement board. And if it's a small-form-factor PC, you won't be able to put a larger ATX motherboard into it. Make sure your case supports the form factor (ATX, MicroATX, and so on) of your new board.
Many older motherboards require a 20-pin main power cable from your power supply, but recent boards require both a 24-pin connector and a separate 4-pin one. Your motherboard won't work if improperly powered, so a new power supply could be in order.
Do your optical and hard drives connect via IDE (usually with ribbon cables) or via newer Serial ATA (thinner cables)? Many newer motherboards have only one IDE port (which supports two drives), whereas older boards have two. If you have more than two IDE drives, be sure your new board has a second IDE connector.
What kind of processor, RAM, and graphics card will you be using? What was top-of-the-line a few years ago could be obsolete today. AGP graphics cards certainly are—most newer motherboards lack slots for them, replacing them with PCI Express (PCIe). Processor socket technology and RAM design have also changed. If you don't want to buy all new components, make sure yours work with the new motherboard. Not sure what you have? A free utility like CPU-Z can suss it out.
Be mindful of Windows' licensing requirements—replacing a motherboard can necessitate reactivating Windows. Depending on whether you have a full-retail or OEM version, you may have to repurchase Windows.
Step 2: Cleaning up
Here, you'll have to make a choice: Install your new motherboard and
keep your existing Windows installation in place, or take the
opportunity to wipe your boot drive and start from scratch. If you do
the second, have your Windows and application discs handy. Either way,
you'll want to back up your data.
Open your case's side and take photos of your PC's rear panel and interior, or label all the cables. (Sticky notes work well.) Many of today's connectors are color-coded, but if yours aren't, this precaution could prevent frustration later.
Once you have all the correct equipment (and a screwdriver), it's time to begin. Disconnect the PC's power cable and everything attached to its rear panel (which is part of the motherboard). Then, turn the case horizontal to tackle the interior.
Ground yourself, either by using an antistatic wrist strap or by touching the metal chassis. Then remove any cards in your old motherboard's expansion slots. Remove the screws securing them to the chassis, then pull the cards straight up and out. (For a PCIe x16 card, you might need to depress a lever on the slot before doing this.) Place them on a clean, static-free surface.
Next, detach all cables and wires connecting your motherboard to the PSU, case front panel, optical and hard drives, or other components (such as fans). For the big PSU power-cable connectors that plug into the motherboard, squeeze a lever on one side to release the connector; most other cables should pull out easily.
Open your case's side and take photos of your PC's rear panel and interior, or label all the cables. (Sticky notes work well.) Many of today's connectors are color-coded, but if yours aren't, this precaution could prevent frustration later.
Once you have all the correct equipment (and a screwdriver), it's time to begin. Disconnect the PC's power cable and everything attached to its rear panel (which is part of the motherboard). Then, turn the case horizontal to tackle the interior.
Ground yourself, either by using an antistatic wrist strap or by touching the metal chassis. Then remove any cards in your old motherboard's expansion slots. Remove the screws securing them to the chassis, then pull the cards straight up and out. (For a PCIe x16 card, you might need to depress a lever on the slot before doing this.) Place them on a clean, static-free surface.
Next, detach all cables and wires connecting your motherboard to the PSU, case front panel, optical and hard drives, or other components (such as fans). For the big PSU power-cable connectors that plug into the motherboard, squeeze a lever on one side to release the connector; most other cables should pull out easily.
Step 3: The great swap-out

Next, pop out the I/O panel—the metal rectangle with the port cutaways—attached to the case. Your new motherboard will come with its own, designed for the board's port arrangement. When inserting the new I/O panel, apply enough pressure around the edges to hear the clicks.
It's more convenient to install the processor, its cooling fan, and the RAM before installing your new motherboard. RAM is easy: Lower the levers on the RAM slots, line up the notch in the module with the slot's protrusion, then press the chip until both levers lock. If you're using two RAM chips, put each in an identically colored slot—this dual-channel architecture increases performance.
Processors are more complicated. Intel's and AMD's designs vary, sometimes between their own lines, but today's processors and sockets are keyed so it's hard to orient a CPU incorrectly. That said, never force anything: If your processor resists when you engage its locking mechanism, you could damage it. Once it's in place, apply a layer of thermal paste to the CPU, and attach the fan to the board, covering the CPU. Don't forget to plug in the fan's power cable to the board's "CPU fan" header.
If your new motherboard is the same size and shape as the old, you shouldn't need to adjust the standoffs that keep the motherboard from touching the case. If, however, you're upgrading from a smaller board to a larger one, you might. Place the motherboard in the case, lining up its holes with the standoffs. Make sure there's a standoff for every hole, and vice versa. After the standoffs are settled, gently place the motherboard, fitting its ports through the I/O panel. Once the holes are directly over the standoffs, secure it using the screws removed earlier
Tuesday, October 9, 2012
How to Fix High CPU Usage

How to Fix High CPU Usage
Posted by john
About High CPU Usage
CPU Usage in Task Manager is 100%
A High CPU Usage reading indicates that the computer's central
processing unit is running at max level or is above normal level for the
number of applications running. Slow performance, hang-ups (freezing),
and random shutdowns are symptoms of high CPU usage. The CPU (processor)
processes all of the instructions for programs. The rate at which CPU's
process instructions in cycles which are measured in hertz (Hz),
commonly extrapolated to megahertz (Mhz) and gigahrtz (Ghz). A given CPU
has a maximum number of cycles which can be produced per second. Simply
put, the CPU can only handle so much before it becomes encumbered by
the number of processes and becomes slow.
Is your computer running extremely slow? Open the Task Manager
(Ctrl+Alt+Del) and check the CPU usage. If your CPU usage stays at 100%
all the time, there is a serious problem. Typically, your processor
usage shouldn't go over 50% unless using large applications such as
video games or media editing programs.
Common
Causes of High CPU Usage
The factors that contribute to high CPU usage and slow performance
are varying. The problem may stem from hardware failure or software
error or both. In order to diagnose the problem accurately, it's a good
idea to know the common causes of high CPU usage so you might better
identify the root cause. Constant, high CPU usage is not normal. If your
computer performs slowly and displays a high CPU usage percentage in
the task manager, there is an underlying problem that is causing the
processor to run at such an extreme speed. Diagnostic troubleshooting is
required to accurately identify the problem, but these are some of the
common causes of high CPU usage:
High CPU Usage May Be Caused By...
- Out-of-date drivers (Run DriverUpdate by SlimWare Utilities or manually update them)
- Running too many applications at once
- Insufficient virtual memory (How to Fix Virtual Memory Issues)
- Overheating/Poor ventilation
- Virus/Malware infections
There are other events which can result in high CPU usage, but
these are some of the most common. We've covered many of them with other
articles or programs linked above. The rest, we have covered in a
detailed guide: Manually Fixing High CPU Usage.
Keep in mind, these guides are meant for users with some administrative
skill and not following them properly can lead to serious issues.
How
to Easily FIX High CPU Usage
Most CPU Usage issues can be traced back to an overload of processes
running, and too little resources to handle all of them. This does not
mean that your computer has to be like this! Rather, you need to find
which processes are clogging up your computer's performance and remedy
them. While this can prove tough to do manually, automated programs such
as FixCleaner can turn this chore into a walk in the park.
FixCleaner is a system optimizer that can seek out issues with your computer's configuration. It's one-click interface allows even the most novice computer users to take advantage of it's high-powered optimization engine. FixCleaner is mainted and supported by SlimWare Utilities Inc, an award-winning software company that has been covered in numerous high-level media publications.
Monday, September 10, 2012
LCD monitor repair
Most of the monitors I use (including this one) are repaired units that
people have discarded or recycled. If you have just a little bit
of tech know-how and a decent parts bin, you can usually get these
discarded monitors running again. This saves space at the
landfill and cuts down on the hazardous waste generation. Plus,
you can donate any extra monitors you have to friends, churches, clubs,
or charities that can use a hand.
And consider taking some fixed monitors down to the city government offices, to discourage them from running reclaiming drives and instead running reuse/repurpose drives!
I recently donated four of my repaired monitors to the local Seniors Center. Lots of people on fixed incomes may have been given a system or had one for several years, but can't afford to replace a monitor that goes out. My afternoon's entertainment fixing a monitor may help someone out of a tight spot
The external power supply
In a surprising number of cases, nothing is wrong with the monitor itself. Those monitors that use a lump-in-the-line or brick power supply usually had a bad supply. If you get an LCD that has a small power jack in the back (like the coaxial power connectors common on most devices), try finding a suitable replacement power supply. You will need to check the ratings for the monitor on the back panel to get the voltage and current required. This is usually something like 12 VDC at 2.0 Amps or so. Go to a surplus shop, root through the junk power supply bin, and find a supply that matches these ratings. Note that going to a larger number on the current (Amps) is OK, but you have to match the voltage exactly!
Note that you must also find a matching power connector! Take the monitor with you when you look for a power supply. When you find a suitable supply, check that the connector on the supply mates properly with the jack on the back of the monitor WITHOUT APPLYING POWER! If the two connectors don't mate, find a second supply with a connector that does mate, even if the voltage or current are wrong. You will later cut the connector off this second supply and splice it onto the cord of the first supply.
When you get home, you have one last item to check before powering up your new monitor. The center pin of the monitor's power jack could be either negative or positive. Whichever it is, your replacement power supply must be wired the same way. If you're lucky, the back of the monitor will give you that information. If it doesn't, use a voltmeter to check the resistance between the center pin and some metal point on the monitor's frame. If you get less than 5 ohms, the jack is wired center-negative (the less common). If you get more than 5 ohms, you should wire your power supply as center-positive.
Compare the polarity your monitor expects to the polarity of the power supply you chose (the one that provides the proper voltage and current). If the power supply plug is the right polarity, it fits, and the voltage/current are correct, you are ready to go; move to the next step where you try out the supply. If the polarity is not correct, you need to cut the power supply output cord (the one with the plug on it) about six inches from the power plug, then rewire the plug with the two wires swapped; be sure to solder your connections and use heatshrink or tape over the splices. If you also need to change the plug by using the second power supply you chose, cut the output wire on the second supply about six inches from the end of its plug and splice the plug onto the output cable of the first supply; be sure to get the polarity right and to solder your connections and use heatshrink or tape over the splices.
Now that your power supply is ready to go, plug it into the monitor, hook the monitor to a PC, plug the power supply into the wall, and boot the PC. If the power supply was the problem, you should see the monitor light up. You're done!
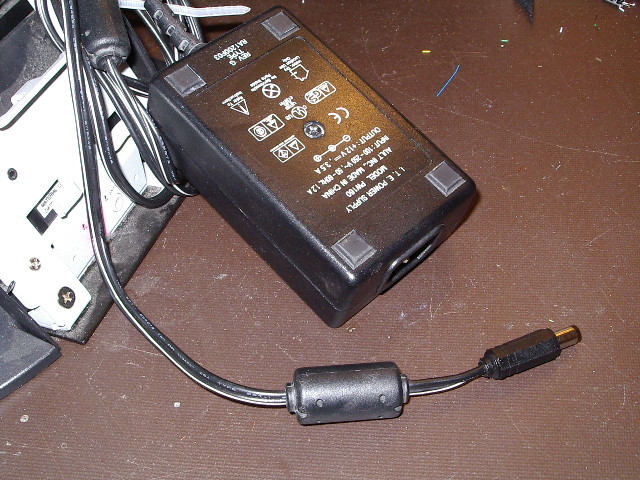
Here I've replaced the plug on an old lump-in-the-line power supply to match a discarded ViewSonic VX500 (a really nice monitor, BTW). The photo shows the voltage and current rating of the supply. I had to solder the two wires from the power supply to match the polarity required by the VX500; it wants center-positive.
120 VAC monitors (and some that use external supplies!)
Often, defective monitors have issues on the main power board. Such monitors can show a wide variety of failures, such as not powering up, flashing the display on and off, or working for a while, then going dark. The first step is to unplug the AC cord, open the back of the monitor, and inspect the power supply board (the board with the largest, heavy-duty components on it). Look for any electrolytic capacitors that are damaged or disfigured in any way. Sometimes you'll see one that has burst its top or that has a bulging top. The top of each electrolytic cap should be flat and shiny. Also look for damage on the bottom of each electrolytic; sometimes these caps will rupture where the leads come out.
If you find a damaged cap, you have to replace it with a similar unit. Note the capacitance and voltage of the bad cap; this will usually be something like 10 uF at 25 VDC. You must use a replacement that has at least the same working voltage and at least the same capacitance. You can go as much above the original voltage as you want, but don't go any more than twice the original capacitance.
IMPORTANT! The replacement capacitor MUST be rated at 105 decC! Do not try to use a cheaper 85 degC capacitor! You can find 105 degC caps at Fry's, Digikey, Mouser, or most TV repair shops or suppliers.
Remove the defective cap, taking care to note the polarity. Electrolytic caps have positive and negative leads and have to be soldered into the circuit with these leads in the proper location; put the replacement cap in the board in the same polarity as the original. Solder the leads in place, then clip them off on the underside of the board so you don't short-circuit something later when you put the monitor back together.
Double-check that there are no more bad caps (you can have two or more bad caps in one monitor). After you have replaced all the bad caps, put the back of the monitor back on, hook up the monitor, and apply power. In most cases, this will fix the monitor.
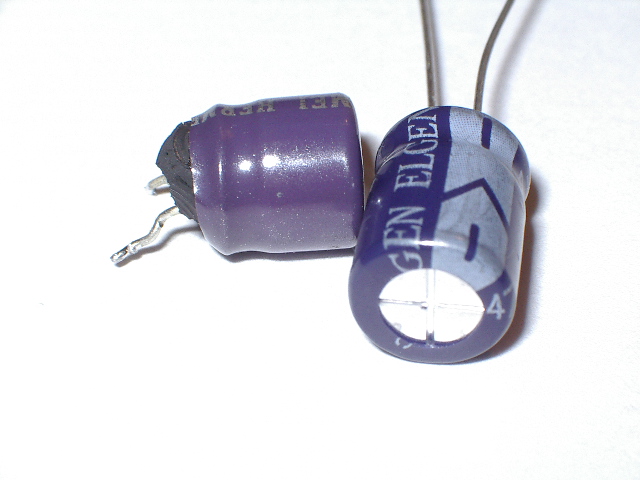
Here you see a bad capacitor on the left and a new capacitor on the right. You can clearly see how the bad cap has burst at the bottom near the leads. All caps in the monitor's power supply should have smooth, flat tops like you see on the new cap. If the top is bulging or burst, replace the cap!
Sometimes, a cap will go bad without bursting or showing any physical damage. One monitor I worked on would run fine for a few seconds, then go dark. It would also smell hot long before it had run long enough to get hot under normal circumstances. After it shut down like this once, I hurriedly reopend the back of the monitor and found a pair of electrolytic caps that were far hotter than anything around them, after only a few seconds of operation. I am waiting for replacement parts, but I strongly suspect these caps were causing the problem.
Note that most power supply boards usually have a very large electrolytic cap somewhere near the 120 VAC connector. I have never seen one of these go bad and comments from repair sites, notably badcaps.net, indicate that this cap almost never fails. Doesn't mean it won't happen, but it seems very unlikely.
Bad solder joints
I am seeing more and more monitors with bad solder joints. I suspect that this is an issue with the move to lead-free solder that was started a few years ago. In years past, the solder joints on five-year old equipment were still bright and shiny. Today, equipment only five years old has grainy, dull, or open solder joints. Typically, ALL of the solder joints on a power supply board are in this condition.
I fixed one monitor where the only problem was a defective solder joint on the main power connector. An easy fix, but it should never have happened.
Part of my routine now is to replace whatever components are obviously defective, then visually inspect (under magnification) all solder joints. I have found the most problems around large-lead parts, such as inductors or through-hole connectors; for some reason, these connections don't age well. To repair such connections, heat the solder joint and suck all of the old lead-free solder from the pad. Then resolder with old-fashioned rosin-core lead solder.
Removing adhesive residue
Sometimes, a store or company will plaster an adhesive label across the screen of a monitor they intend to dump. This always irritates me; just because they can't/won't fix it, why do they have to make it that much harder for someone else to work on the unit?
Regardless, you can clean up the monitor screen easily. First, carefully peel away all of the paper label that you can. DO NOT use a knife or other sharp instrument! Just carefully scrape the paper away with your fingernail. Don't try to scrape off the adhesive, you'll just mar or damage the screen.
When you have as much of the paper removed as you can, set the monitor flat on a table with the screen facing up. Carefully pour just enough olive oil or other light vegetable oil on the screen to cover the adhesive. You want a small pool of oil completely covering the adhesive. Make sure none of the oil drips into the seams of the frame or you'll have to disassemble the unit to clean out the oil. Leave the oil sitting on the surface of the monitor for at least an hour.
Mop up the oil with a soft paper towel. Then wipe the screen with a soft paper towel that has been dampened with water and a small amount of liquid hand soap. Follow this by wiping the screen with a dampened paper towel (water only). Finally, clean the screen with Windex and a soft paper towel.
If there is still adhesive left on the screen, just repeat the oiling and cleaning treatment.
Nothing wrong!
One recent monitor, a CTL 170Lx 17-inch unit, actually didn't have anything wrong with it at all! When I applied power, the screen stayed dark but the little LED on the frame would blink green, then yellow, then green, over and over. I did some web searches and discovered that this monitor sometimes gets confused after a power-surge or power failure. To recover, I had to reset the monitor by holding down front-panel buttons two and three (counting from the left) while powering up the unit, then wait until the LED stopped blinking. Once I did that, the monitor worked perfectly! You don't often get LCDs that are this simple to repair, but it never hurts to check the web; it could save you the hassle of opening up a perfectly working monitor.
(Props to Chris McLellen of Boise LCD for this reset tip. Chris has a nice website and looks like he offers a good service. I haven't done business with him, but I like the attitude he shows and the fact he was willing to blog this very helpful tip for all to use. Thanks, Chris!)
Worst case
The above paragraphs describe the problems with maybe 75% of the monitors I've fixed. But sometimes you get a monitor that doesn't work after trying these suggestions. At this point, you may need to find someone with more troubleshooting skills and tools than you have. Check the local vocational college, repair shops, or high-tech clubs and see what you can do. At the worst, you will end up discarding this monitor, which is how you got it in the first place.
If you do choose to discard, PLEASE try to find a good home for the monitor! See if there is a local Freecycle or high-tech collection point that will hopefully get your monitor into the hands of someone who CAN fix it and CAN reuse/repurpose it.
Monitors I've rescued...
Here are some examples of monitors I've repaired, complete with the stories behind them.
Planar
I found this monitor at RE-PC in Tukwilla several months ago. This 17" monitor has a coax power connector on the back panel, so I started out by making a new wall-wart power supply with matching cable. However, when I plugged in the cable, the monitor still didn't work, so I had to open the back and take a look. I did not see any damaged or burned components, so I hooked up the power supply and started tracing voltages. Oddly, there was no voltage present on the PCB, even though the wall-wart power supply was working. Turned out the coax power jack was defective. I replaced it with one from my junk box and the monitor lit right up. Until I got the Dell 1905FP (below), this has been my best and favorite monitor. I think I paid $7 for it...
I picked up this 19" monitor at RE-PC in Tukwilla for $10. This monitor has a 120 VAC connector on the back, so I figured I'd find bad caps in the power supply. When I opened up the unit, I noticed three capacitors on the power supply board were distorted. All three caps were 1000 uf at 10VDC. I didn't have any of these in my parts bin, so I motored down to Vetco in Redmond and picked up those caps plus a good assortment of other values to keep my junk box stocked. Vetco's prices are a bit high, but the quality is the best. You gotta love being able to walk into a parts store and load up on Nichicon 105 degC electrolytics on a Sunday afternoon!
I replaced the caps, put the unit back together, and fired it up; works like a champ. This model is no longer stocked by Dell, but a search on the Internet shows it goes for about $250 new. Highest normal setting is 1280x1024 resolution at 75 Hz refresh, which is certainly useable. The colors are rich and the stand it came with has smooth, sure motion. Not bad for $15 (monitor plus caps).
I bought this non-working 19" monitor at PC Recycle in Bellevue for $10. It uses a 120 VAC power cord, but plugging it in yielded nothing, not even a lit power LED. I opened the case and immediately noticed that all of the solder joints had a grey, grainy look to them. In the days of leaded solder, I would have called all of them bad solder joints. Now that we're using lead-free solder, I guess this is as good as it gets.
I replaced three caps in the power supply board; one was obviously bad, and I replaced the other two just because. When I applied power, the unit still didn't turn on.
Next up was resoldering the AC power connector on the main board. I didn't see anything obviously wrong, but I have had such connections go bad before. When I resoldered the pins, I made sure to use leaded solder. When I applied power, still no joy.
I checked voltages at the computer board and everything looked good. It seemed logical then that the signals from the computer board weren't making it to the graphics connection on the LCD panel. I reseated the small multi-pin connector at the LCD panel. I also reheated all of the pins for that connector on the underside of the computer board. When I applied power, I had a beautiful LCD display.
Unforutantely, I can't say definitely that the fault lay with the solder joints on the underside of the computer board. I suspect that was the culprit, but I can't prove it. Oh well. $16 and a couple of entertaining hours, and I have a new monitor. Great way to spend an afternoon.
Another $10 purchase from PC Recycle. This monitor uses a 120 VAC power cord; when first powered up, it showed the AOC logo and a Windows display for about ten seconds, then the screen went dark. I opened up the power supply and did not find any suspicious-looking caps, but I replaced the three highest-value electrolytics on the PCB anyway, in the "it can't hurt" philosophy. Unfortunately, it also didn't fix the problem. It wasn't that the screen stopped receiving graphics signals from the processor board; the drive voltage to the backlights was cutting out.
Research on the web turned up a reference to inductors on the power supply board of this model occasionally showing bad solder joints. A quick look showed everything seemed fine. However, a closer inspection under magnification showed that the solder joints for both L201 and L202 appeared to have aged badly; one of them was clearly open. I sucked the solder from each connection and resoldered it; problem fixed.
This monitor has an excellent picture with good color, supports 1280x1024. It also rotates 90 degrees on its stand, but I don't have drivers to support that feature yet.
This is a second LM729 monitor I picked up at the same time as above, also for $10. It showed the same problems as the first one, so I was filled with confidence as I opened it up. Again, all of the caps looked perfect. This time, I went straight for the two inductors on the power supply board. As before, the solder joints for both had a grainy appearance and while I've seen worse, I resoldered them anyway. I also touched up several other connections, notably those on a pair of power transistors nearby. Plugged the monitor into a test PC I keep handy; monitor worked like a charm.
I find it odd that so many monitor makers can't get the caps right, but AOC did. However, AOC had problems with solder joints aging on the inductors where other makers don't. Regardless, to the consumer the issue looks the same; the monitor stops working. Oh well...
Viewsonic VA902b (added 27 Mar 2011)
I was in the Arlington PC Recycle and picked up this unit for $19. This is a no-frills 19" monitor; no speakers, no DVI connector, no USB. When I plugged it in and fed it a graphics signal, the monitor would work fine for a second or two, go dark for a couple of seconds, then repeat the cycle continuously. When I opened it up, I found and replaced two bulging caps (1000uf/25V and 220uf/25V). I also replaced a second 220uf/25V cap in the same area, just because. I double-checked the solder joints on the underside of the power supply board and resoldered several that looked grainy. Reassembled the monitor, plugged it in, looks great! Total cost: about $23.
Dell 2005FPW (added 10 Apr 2011)
This was a $20 purchase from the Arlington PC REcycle. This is a nice, 20" wide-screen monitor, no speakers, with DVI and USB connectors. When I powered this one up, it showed an excellent graphics picture for about three minutes, then the screen went black. After a few seconds, the graphics image came back on, but again when out after a few seconds. I replaced ALL of the electrolytics on the power boards EXCEPT the largest cap near the AC connector. The symptoms improved slightly, in that it took longer before the screen first went black, but the problem persisted.
Research on the web shows that two caps on the logic board (C637 and C635) are often at fault, so I replaced them; problem remained. I replaced a couple other caps in the same area on the logic board, but the problem was still there.
I soldered a wire to the GND connection and a wire to the 12 VDC connection (pin 1) on the power supply board, partially reassembled the display, then powered up the display with a meter on the wires so I could monitor the value of the 12 VDC supply to the logic board. The 12 VDC supply started out at about 6.35 VDC. This voltage slowly dropped until it hit about 6.01 VDC, at which point the monitor went dark. The supply voltage immediately started climbing until it hit about 6.14 VDC. At this point, the display came back on, the supply voltage dropped back to 6.01 VDC, and the display went dark again. This cycle repeated until I shut off power.
I unsoldered the 12 VDC regulator (a KIA278R12) from the power board and removed it from its heatsink. On my bench, applying 12.5 VDC to the input gave me 7.5 VDC output with no load, so the regulator is shot. I was able to find a suitable replacement from Mouser (the Fairchild KA378R12C) and have some on order. The Fairchild part is a 3A regulator and should prove more robust than the 2A part it is replacing.
More on this fix later...
OK, I received the KA378R12C regulators. The first thing I did was hook one up on my bench and check the output. As expected, it outputs 12 VDC. I spread a little heatsink compound on the device's back, bolted the regulator to the original heatsink, and put the monitor back together. Works like a champ (I'm using it to write this update).
This monitor was a bear to take apart and put back together. I ended up loosening the adhesive tape that holds the flat ribbon cable connecting the front-panel switch board, to give myself a little bit of extra slack for putting the front panel back together. Even so, this is an awkward monitor to work on. Hopefully, I've dealt with all the issues and won't have to reopen it for a long time.
I picked up this 19" plain-Jane (Dsub-15 VGA only) monitor from the IT department of a local business. It was out of warranty and had been stuck on a shelf, waiting for the recycler. I didn't even bother to power it up so I don't know why it was labeled BAD with a big sticker on the screen. The power supply board had three bad caps, a pair of 680uf/16VDC and a 330uf/35VDC. I replaced them with suitable units from my parts bin, put the monitor back together, and it powered up just fine. This unit has a very nice image with good color; it will make a great utility display. Another one saved from the recycler!
Another orphan rescued from a local business, this 19" monitor is loaded with VGA, DVI and USB connectors. As above, I didn't even power this one up, so I don't know what the symptoms were. This fix required replacing four 330uf/35VDC caps. I didn't have that many such caps in my parts box, but a quick trip to Vetco (on Sunday!) took care of that. While I had the unit open, I wiped the two major heatsinks free of thermal compound, then replaced the compound with new from a tube I keep in my parts bin. I also reheated a couple of suspicious looking solder joints on the power board. The repaired monitor has excellent color and brightness, and will make a nice addition to my computer room.
And consider taking some fixed monitors down to the city government offices, to discourage them from running reclaiming drives and instead running reuse/repurpose drives!
I recently donated four of my repaired monitors to the local Seniors Center. Lots of people on fixed incomes may have been given a system or had one for several years, but can't afford to replace a monitor that goes out. My afternoon's entertainment fixing a monitor may help someone out of a tight spot
The external power supply
In a surprising number of cases, nothing is wrong with the monitor itself. Those monitors that use a lump-in-the-line or brick power supply usually had a bad supply. If you get an LCD that has a small power jack in the back (like the coaxial power connectors common on most devices), try finding a suitable replacement power supply. You will need to check the ratings for the monitor on the back panel to get the voltage and current required. This is usually something like 12 VDC at 2.0 Amps or so. Go to a surplus shop, root through the junk power supply bin, and find a supply that matches these ratings. Note that going to a larger number on the current (Amps) is OK, but you have to match the voltage exactly!
Note that you must also find a matching power connector! Take the monitor with you when you look for a power supply. When you find a suitable supply, check that the connector on the supply mates properly with the jack on the back of the monitor WITHOUT APPLYING POWER! If the two connectors don't mate, find a second supply with a connector that does mate, even if the voltage or current are wrong. You will later cut the connector off this second supply and splice it onto the cord of the first supply.
When you get home, you have one last item to check before powering up your new monitor. The center pin of the monitor's power jack could be either negative or positive. Whichever it is, your replacement power supply must be wired the same way. If you're lucky, the back of the monitor will give you that information. If it doesn't, use a voltmeter to check the resistance between the center pin and some metal point on the monitor's frame. If you get less than 5 ohms, the jack is wired center-negative (the less common). If you get more than 5 ohms, you should wire your power supply as center-positive.
Compare the polarity your monitor expects to the polarity of the power supply you chose (the one that provides the proper voltage and current). If the power supply plug is the right polarity, it fits, and the voltage/current are correct, you are ready to go; move to the next step where you try out the supply. If the polarity is not correct, you need to cut the power supply output cord (the one with the plug on it) about six inches from the power plug, then rewire the plug with the two wires swapped; be sure to solder your connections and use heatshrink or tape over the splices. If you also need to change the plug by using the second power supply you chose, cut the output wire on the second supply about six inches from the end of its plug and splice the plug onto the output cable of the first supply; be sure to get the polarity right and to solder your connections and use heatshrink or tape over the splices.
Now that your power supply is ready to go, plug it into the monitor, hook the monitor to a PC, plug the power supply into the wall, and boot the PC. If the power supply was the problem, you should see the monitor light up. You're done!
Here I've replaced the plug on an old lump-in-the-line power supply to match a discarded ViewSonic VX500 (a really nice monitor, BTW). The photo shows the voltage and current rating of the supply. I had to solder the two wires from the power supply to match the polarity required by the VX500; it wants center-positive.
120 VAC monitors (and some that use external supplies!)
Often, defective monitors have issues on the main power board. Such monitors can show a wide variety of failures, such as not powering up, flashing the display on and off, or working for a while, then going dark. The first step is to unplug the AC cord, open the back of the monitor, and inspect the power supply board (the board with the largest, heavy-duty components on it). Look for any electrolytic capacitors that are damaged or disfigured in any way. Sometimes you'll see one that has burst its top or that has a bulging top. The top of each electrolytic cap should be flat and shiny. Also look for damage on the bottom of each electrolytic; sometimes these caps will rupture where the leads come out.
If you find a damaged cap, you have to replace it with a similar unit. Note the capacitance and voltage of the bad cap; this will usually be something like 10 uF at 25 VDC. You must use a replacement that has at least the same working voltage and at least the same capacitance. You can go as much above the original voltage as you want, but don't go any more than twice the original capacitance.
IMPORTANT! The replacement capacitor MUST be rated at 105 decC! Do not try to use a cheaper 85 degC capacitor! You can find 105 degC caps at Fry's, Digikey, Mouser, or most TV repair shops or suppliers.
Remove the defective cap, taking care to note the polarity. Electrolytic caps have positive and negative leads and have to be soldered into the circuit with these leads in the proper location; put the replacement cap in the board in the same polarity as the original. Solder the leads in place, then clip them off on the underside of the board so you don't short-circuit something later when you put the monitor back together.
Double-check that there are no more bad caps (you can have two or more bad caps in one monitor). After you have replaced all the bad caps, put the back of the monitor back on, hook up the monitor, and apply power. In most cases, this will fix the monitor.
Here you see a bad capacitor on the left and a new capacitor on the right. You can clearly see how the bad cap has burst at the bottom near the leads. All caps in the monitor's power supply should have smooth, flat tops like you see on the new cap. If the top is bulging or burst, replace the cap!
Sometimes, a cap will go bad without bursting or showing any physical damage. One monitor I worked on would run fine for a few seconds, then go dark. It would also smell hot long before it had run long enough to get hot under normal circumstances. After it shut down like this once, I hurriedly reopend the back of the monitor and found a pair of electrolytic caps that were far hotter than anything around them, after only a few seconds of operation. I am waiting for replacement parts, but I strongly suspect these caps were causing the problem.
Note that most power supply boards usually have a very large electrolytic cap somewhere near the 120 VAC connector. I have never seen one of these go bad and comments from repair sites, notably badcaps.net, indicate that this cap almost never fails. Doesn't mean it won't happen, but it seems very unlikely.
Bad solder joints
I am seeing more and more monitors with bad solder joints. I suspect that this is an issue with the move to lead-free solder that was started a few years ago. In years past, the solder joints on five-year old equipment were still bright and shiny. Today, equipment only five years old has grainy, dull, or open solder joints. Typically, ALL of the solder joints on a power supply board are in this condition.
I fixed one monitor where the only problem was a defective solder joint on the main power connector. An easy fix, but it should never have happened.
Part of my routine now is to replace whatever components are obviously defective, then visually inspect (under magnification) all solder joints. I have found the most problems around large-lead parts, such as inductors or through-hole connectors; for some reason, these connections don't age well. To repair such connections, heat the solder joint and suck all of the old lead-free solder from the pad. Then resolder with old-fashioned rosin-core lead solder.
Removing adhesive residue
Sometimes, a store or company will plaster an adhesive label across the screen of a monitor they intend to dump. This always irritates me; just because they can't/won't fix it, why do they have to make it that much harder for someone else to work on the unit?
Regardless, you can clean up the monitor screen easily. First, carefully peel away all of the paper label that you can. DO NOT use a knife or other sharp instrument! Just carefully scrape the paper away with your fingernail. Don't try to scrape off the adhesive, you'll just mar or damage the screen.
When you have as much of the paper removed as you can, set the monitor flat on a table with the screen facing up. Carefully pour just enough olive oil or other light vegetable oil on the screen to cover the adhesive. You want a small pool of oil completely covering the adhesive. Make sure none of the oil drips into the seams of the frame or you'll have to disassemble the unit to clean out the oil. Leave the oil sitting on the surface of the monitor for at least an hour.
Mop up the oil with a soft paper towel. Then wipe the screen with a soft paper towel that has been dampened with water and a small amount of liquid hand soap. Follow this by wiping the screen with a dampened paper towel (water only). Finally, clean the screen with Windex and a soft paper towel.
If there is still adhesive left on the screen, just repeat the oiling and cleaning treatment.
Nothing wrong!
One recent monitor, a CTL 170Lx 17-inch unit, actually didn't have anything wrong with it at all! When I applied power, the screen stayed dark but the little LED on the frame would blink green, then yellow, then green, over and over. I did some web searches and discovered that this monitor sometimes gets confused after a power-surge or power failure. To recover, I had to reset the monitor by holding down front-panel buttons two and three (counting from the left) while powering up the unit, then wait until the LED stopped blinking. Once I did that, the monitor worked perfectly! You don't often get LCDs that are this simple to repair, but it never hurts to check the web; it could save you the hassle of opening up a perfectly working monitor.
(Props to Chris McLellen of Boise LCD for this reset tip. Chris has a nice website and looks like he offers a good service. I haven't done business with him, but I like the attitude he shows and the fact he was willing to blog this very helpful tip for all to use. Thanks, Chris!)
Worst case
The above paragraphs describe the problems with maybe 75% of the monitors I've fixed. But sometimes you get a monitor that doesn't work after trying these suggestions. At this point, you may need to find someone with more troubleshooting skills and tools than you have. Check the local vocational college, repair shops, or high-tech clubs and see what you can do. At the worst, you will end up discarding this monitor, which is how you got it in the first place.
If you do choose to discard, PLEASE try to find a good home for the monitor! See if there is a local Freecycle or high-tech collection point that will hopefully get your monitor into the hands of someone who CAN fix it and CAN reuse/repurpose it.
Monitors I've rescued...
Here are some examples of monitors I've repaired, complete with the stories behind them.
Planar
I found this monitor at RE-PC in Tukwilla several months ago. This 17" monitor has a coax power connector on the back panel, so I started out by making a new wall-wart power supply with matching cable. However, when I plugged in the cable, the monitor still didn't work, so I had to open the back and take a look. I did not see any damaged or burned components, so I hooked up the power supply and started tracing voltages. Oddly, there was no voltage present on the PCB, even though the wall-wart power supply was working. Turned out the coax power jack was defective. I replaced it with one from my junk box and the monitor lit right up. Until I got the Dell 1905FP (below), this has been my best and favorite monitor. I think I paid $7 for it...
I picked up this 19" monitor at RE-PC in Tukwilla for $10. This monitor has a 120 VAC connector on the back, so I figured I'd find bad caps in the power supply. When I opened up the unit, I noticed three capacitors on the power supply board were distorted. All three caps were 1000 uf at 10VDC. I didn't have any of these in my parts bin, so I motored down to Vetco in Redmond and picked up those caps plus a good assortment of other values to keep my junk box stocked. Vetco's prices are a bit high, but the quality is the best. You gotta love being able to walk into a parts store and load up on Nichicon 105 degC electrolytics on a Sunday afternoon!
I replaced the caps, put the unit back together, and fired it up; works like a champ. This model is no longer stocked by Dell, but a search on the Internet shows it goes for about $250 new. Highest normal setting is 1280x1024 resolution at 75 Hz refresh, which is certainly useable. The colors are rich and the stand it came with has smooth, sure motion. Not bad for $15 (monitor plus caps).
I bought this non-working 19" monitor at PC Recycle in Bellevue for $10. It uses a 120 VAC power cord, but plugging it in yielded nothing, not even a lit power LED. I opened the case and immediately noticed that all of the solder joints had a grey, grainy look to them. In the days of leaded solder, I would have called all of them bad solder joints. Now that we're using lead-free solder, I guess this is as good as it gets.
I replaced three caps in the power supply board; one was obviously bad, and I replaced the other two just because. When I applied power, the unit still didn't turn on.
Next up was resoldering the AC power connector on the main board. I didn't see anything obviously wrong, but I have had such connections go bad before. When I resoldered the pins, I made sure to use leaded solder. When I applied power, still no joy.
I checked voltages at the computer board and everything looked good. It seemed logical then that the signals from the computer board weren't making it to the graphics connection on the LCD panel. I reseated the small multi-pin connector at the LCD panel. I also reheated all of the pins for that connector on the underside of the computer board. When I applied power, I had a beautiful LCD display.
Unforutantely, I can't say definitely that the fault lay with the solder joints on the underside of the computer board. I suspect that was the culprit, but I can't prove it. Oh well. $16 and a couple of entertaining hours, and I have a new monitor. Great way to spend an afternoon.
Another $10 purchase from PC Recycle. This monitor uses a 120 VAC power cord; when first powered up, it showed the AOC logo and a Windows display for about ten seconds, then the screen went dark. I opened up the power supply and did not find any suspicious-looking caps, but I replaced the three highest-value electrolytics on the PCB anyway, in the "it can't hurt" philosophy. Unfortunately, it also didn't fix the problem. It wasn't that the screen stopped receiving graphics signals from the processor board; the drive voltage to the backlights was cutting out.
Research on the web turned up a reference to inductors on the power supply board of this model occasionally showing bad solder joints. A quick look showed everything seemed fine. However, a closer inspection under magnification showed that the solder joints for both L201 and L202 appeared to have aged badly; one of them was clearly open. I sucked the solder from each connection and resoldered it; problem fixed.
This monitor has an excellent picture with good color, supports 1280x1024. It also rotates 90 degrees on its stand, but I don't have drivers to support that feature yet.
This is a second LM729 monitor I picked up at the same time as above, also for $10. It showed the same problems as the first one, so I was filled with confidence as I opened it up. Again, all of the caps looked perfect. This time, I went straight for the two inductors on the power supply board. As before, the solder joints for both had a grainy appearance and while I've seen worse, I resoldered them anyway. I also touched up several other connections, notably those on a pair of power transistors nearby. Plugged the monitor into a test PC I keep handy; monitor worked like a charm.
I find it odd that so many monitor makers can't get the caps right, but AOC did. However, AOC had problems with solder joints aging on the inductors where other makers don't. Regardless, to the consumer the issue looks the same; the monitor stops working. Oh well...
Viewsonic VA902b (added 27 Mar 2011)
I was in the Arlington PC Recycle and picked up this unit for $19. This is a no-frills 19" monitor; no speakers, no DVI connector, no USB. When I plugged it in and fed it a graphics signal, the monitor would work fine for a second or two, go dark for a couple of seconds, then repeat the cycle continuously. When I opened it up, I found and replaced two bulging caps (1000uf/25V and 220uf/25V). I also replaced a second 220uf/25V cap in the same area, just because. I double-checked the solder joints on the underside of the power supply board and resoldered several that looked grainy. Reassembled the monitor, plugged it in, looks great! Total cost: about $23.
Dell 2005FPW (added 10 Apr 2011)
This was a $20 purchase from the Arlington PC REcycle. This is a nice, 20" wide-screen monitor, no speakers, with DVI and USB connectors. When I powered this one up, it showed an excellent graphics picture for about three minutes, then the screen went black. After a few seconds, the graphics image came back on, but again when out after a few seconds. I replaced ALL of the electrolytics on the power boards EXCEPT the largest cap near the AC connector. The symptoms improved slightly, in that it took longer before the screen first went black, but the problem persisted.
Research on the web shows that two caps on the logic board (C637 and C635) are often at fault, so I replaced them; problem remained. I replaced a couple other caps in the same area on the logic board, but the problem was still there.
I soldered a wire to the GND connection and a wire to the 12 VDC connection (pin 1) on the power supply board, partially reassembled the display, then powered up the display with a meter on the wires so I could monitor the value of the 12 VDC supply to the logic board. The 12 VDC supply started out at about 6.35 VDC. This voltage slowly dropped until it hit about 6.01 VDC, at which point the monitor went dark. The supply voltage immediately started climbing until it hit about 6.14 VDC. At this point, the display came back on, the supply voltage dropped back to 6.01 VDC, and the display went dark again. This cycle repeated until I shut off power.
I unsoldered the 12 VDC regulator (a KIA278R12) from the power board and removed it from its heatsink. On my bench, applying 12.5 VDC to the input gave me 7.5 VDC output with no load, so the regulator is shot. I was able to find a suitable replacement from Mouser (the Fairchild KA378R12C) and have some on order. The Fairchild part is a 3A regulator and should prove more robust than the 2A part it is replacing.
More on this fix later...
OK, I received the KA378R12C regulators. The first thing I did was hook one up on my bench and check the output. As expected, it outputs 12 VDC. I spread a little heatsink compound on the device's back, bolted the regulator to the original heatsink, and put the monitor back together. Works like a champ (I'm using it to write this update).
This monitor was a bear to take apart and put back together. I ended up loosening the adhesive tape that holds the flat ribbon cable connecting the front-panel switch board, to give myself a little bit of extra slack for putting the front panel back together. Even so, this is an awkward monitor to work on. Hopefully, I've dealt with all the issues and won't have to reopen it for a long time.
I picked up this 19" plain-Jane (Dsub-15 VGA only) monitor from the IT department of a local business. It was out of warranty and had been stuck on a shelf, waiting for the recycler. I didn't even bother to power it up so I don't know why it was labeled BAD with a big sticker on the screen. The power supply board had three bad caps, a pair of 680uf/16VDC and a 330uf/35VDC. I replaced them with suitable units from my parts bin, put the monitor back together, and it powered up just fine. This unit has a very nice image with good color; it will make a great utility display. Another one saved from the recycler!
Another orphan rescued from a local business, this 19" monitor is loaded with VGA, DVI and USB connectors. As above, I didn't even power this one up, so I don't know what the symptoms were. This fix required replacing four 330uf/35VDC caps. I didn't have that many such caps in my parts box, but a quick trip to Vetco (on Sunday!) took care of that. While I had the unit open, I wiped the two major heatsinks free of thermal compound, then replaced the compound with new from a tube I keep in my parts bin. I also reheated a couple of suspicious looking solder joints on the power board. The repaired monitor has excellent color and brightness, and will make a nice addition to my computer room.
Monday, September 3, 2012
SAVE YOUR DATA CAREFULLY
SAVE YOUR DATA CAREFULLY

Did
you know? That something very valuable from a computer is a data. Why
do I say that? Because as we know, if we have so many files that are
very important, this must we look. This is damage a computer we cannot
be predicted in advance. Therefore if we would that have on the backup data and files on our computer.
There are so many ways that we can use to make back up your data, back
up both the data offline, such as using the CD, and back up data online
through the Internet facilities, whether it is paid or free. However, if
the computer damage that we have going on your hard disk, and we cannot
repair it, then we can use the services of data recovery to save data or files that are on the hard disk is.
Usually to identify the signs of damage on a hard disk
there are two types of damage, the damage to hardware and software
damage. Damage to the hardware is usually more going on the hard disk in
the disk. Damage like this is often referred to the physical damage.
And this type of damage is usually very difficult to regenerate. While
the software for the damage usually occurs on the setup disc format that
happens when we do run the computer. This we can recognize at the time
of booting process, usually when booting process is to take a very long
time, it can be hard disk boot sector is damaged.
Usually there are differences in the data recovery,
namely the base operating system with Windows and if we use Mac OS, we
can MAC data recovery service. For that you should really consider this,
if the computer you are using one of the two is operating system. If we
want to use data recovery services online, there are several
things we should note, are the types of services they provide, whether
using the system one way service, or use the system with the server data
recovery, this very effect on the type of data you want to save.
PROTECT YOUR COMPUTURE FROM VIRUSES

If
we like to play games, then we must also protect our PC from virus
attacks. Election must see how the various considerations, between which
is the use of light resources, ability to detect the virus, the
handling of the virus, the update that is flexible, the start up
process, and so forth. Norton, Symantec's product is quite a lot of
complaints by users because of the use of the resources that...
PROTECT YOUR LAPTOP FROM VIRUSES

Protect
it better than cure, so your laptop should be protected from virus
attacks. If your laptop often interacts with the Internet, the
possibility of thousands of virus will try to enter your laptop system.
Indeed facilitate the spread of Internet viruses, especially at this
time; a virus can spread itself to all the network computer in the
network in just seconds. There are several steps to anticipate...
ANTIVIRUS 2009

Since
the virus that is disbursed through the Internet, the antivirus service
is also growing rapidly. Indeed, all existing antivirus capabilities to
offer protection against computer system. Currently, there is some
antivirus software that is quite good and effective in protecting your
computer system. Some antivirus software is familiar to users of laptop
or desktop PC. AVG 8.0 If you want a free...
PC SECURE FROM SPYWARE

Internet
access is increasingly spyware creators make much more freely run. It
is not spyware virus or worm, but what spyware is far more dangerous,
because he was spy that you continue to lurk system. Even without the
Internet spyware can be installed by someone to spy on all that you do.
Moreover, when the system was connected to the Internet, then all
activities you will easily be from the distance,...
ANTIVIRUS

Antivirus
software for computers must be there. Because of computer viruses
currently more vicious and variety. What's wrong? among other reasons,
more and more people utilize the Internet connection. On the other hand,
the creator of the virus found more clever ways to attack system. While
sophisticated operating system is also more complicated to be regulated
so you need a security update as often...
HOW TO REPAIR MOTHERBOARD ?
HOW TO REPAIR MOTHERBOARD ?

Motherboard is a board / main board where the components such as microprocessor and main memory (RAM, ROM, BIOS)
chip along with other controllers. There are also slots Expansion is
the place to install the card-card additional work to improve the
facilities and capabilities that are required. Microprocessor inserted
in the socket / slot that matches the shape and size of microprocessor,
such as socket 370, 470, LGA 775 socket, a socket 462 (AMD), the socket slot I (Pentium 2 and 3).
In the motherboard, microprocessor
to communicate with other components through a bus or data path. This
bus has been developed from the bus 66, 100, 133, 200, 266, 333, 400,
500, 800 MHz. The development of this work to compensate for the
microprocessor is faster. Slot expansion development experience. Table
diagram motherboard has usually included when you buy the CPU.
Total off
Check the power supply : In the situation in the offshore power cable from the power supply, cable release socket is inserted in the ATX1. Once released, re-pair power cable, connect / cable green with black cable, check that the fan rotates in the power supply? If the rotary power supply means good. Loose cable connections before re-install and re-ATX1 cable to the motherboard. Check the Clear CMOS Jumper, whether in position or Clear Free, usually when a new motherboard, the CMOS jumpers position in the Clear position.
Check the power supply : In the situation in the offshore power cable from the power supply, cable release socket is inserted in the ATX1. Once released, re-pair power cable, connect / cable green with black cable, check that the fan rotates in the power supply? If the rotary power supply means good. Loose cable connections before re-install and re-ATX1 cable to the motherboard. Check the Clear CMOS Jumper, whether in position or Clear Free, usually when a new motherboard, the CMOS jumpers position in the Clear position.
Check
IC chip set is connected, and in the Switch On, whether or not
excessive heat, over heat means Chip set is already damaged. CMOS IC for
part time until the sale is not free. Check also whether the switch on
its work. Loading motherboard is carefully, you try to use clean liquid,
if can not use liquid bottle in a container. After you blow-dry clean.
Replace the IC regulator which is located around the socket on the motherboard Power. Change capacity
of 1000 s / d 3300 UF / 10 Volt located around the power connector on
the motherboard. Be careful to ensure that the component pieces attach
power cable not connected to electricity.
But not shown flame
You try and see if anyone listened to the sound of a voice . If there are, the damage usually is in the processor, memory and VGA. Check Processor, you try to grasp whether excessive heat or cold? If excessive heat means the processor fan is not working properly then you will change, but if the processor does not mean that the cold work alias is broken.
But not shown flame
You try and see if anyone listened to the sound of a voice . If there are, the damage usually is in the processor, memory and VGA. Check Processor, you try to grasp whether excessive heat or cold? If excessive heat means the processor fan is not working properly then you will change, but if the processor does not mean that the cold work alias is broken.
Check
memory, if memory is usually broken voice heard on the speaker of 3
times. In the dead, pull the memory pin use clean pencil eraser to
clean, and then install it again. If it still means that there is a
damaged one of the IC is damaged. Check VGA Card, VGA Card pull
in the dead / off you try to press, there is less likelihood of entry or
try to clean your feet / pin it. If the VGA card fans, clean the fan.
Still
does not appear if you try to check perhaps monitor that is not a
flame, to ensure that broken monitor or CPU, you try to press keys on
the keyboard, whether light is glowing or not. If the flame means
damage to the CPU. Which is the default if I fix Computers, I always
cleared of dust, whether it is the motherboard, memory, cdrom, floppy disk,
etc., because it is very influential in the computer again if the dirty
/ old is not clean. But you must be careful in the process and do not
hurry.
Hang and Often Off
Check the Power Supply, try to use another power supply that is still me to restart or hang them. If after the power supply was replaced normal / good, the powers supply problems. Change course because even if I can regenerate themselves are unsure what can still work well, because the power supply is a vital component. Moreover, at this time the price for power supply to cheap, I suggest to change it.
Check the Power Supply, try to use another power supply that is still me to restart or hang them. If after the power supply was replaced normal / good, the powers supply problems. Change course because even if I can regenerate themselves are unsure what can still work well, because the power supply is a vital component. Moreover, at this time the price for power supply to cheap, I suggest to change it.
Check whether the virus, anti-virus program should always be installed and enable the auto protect it. I usually use Norton Anti virus. You need to frequently update your anti virus because if there is a new virus variants, anti-virus while you detect the virus. At the time of hang and have blue screen message such as "error at address ..." there is usually a problem in memory. Clean the memory as the above step.
Try re-installing your Windows
If it still hangs / me try to restart your own check on the motherboard, you see the physical changes in the components, especially capacitor, a rounded black shapes have any posts 10 Volt capacity between 1000 s / d 3300 10 volt, usually visible, if the visible damage / swelling and remove liquids or rust.
If it still hangs / me try to restart your own check on the motherboard, you see the physical changes in the components, especially capacitor, a rounded black shapes have any posts 10 Volt capacity between 1000 s / d 3300 10 volt, usually visible, if the visible damage / swelling and remove liquids or rust.
Sunday, September 2, 2012
JE KAMA DVD TRAY YA LAPTOP IMEFAIL KUFUNGUKA UTAFANYAJA?., NJOO NA FUATILIA HAPA
There are quite a few reasons the DVD tray in your laptop might fail to open when you hit the eject button. About the worst thing it can be is if the motor or gear train failed, which would mean replacing the drive. If the disc in the drive plays OK, you know that the power and the connector are fine. If not, you should try reseating the drive in the bay. It's also possible for the drive to be locked in software by the operating system, or for a power management scheme to have cut power to the drive. Check these by right clicking the drive icon and checking properties, or looking at you power management settings. But, when all else fails and you can't get the disc out of the drive, there's always, THE MIGHTY PAPERCLIP. |
![]() |
![]() |
CD and DVD drives for computers have been designed with an emergency release mechanism since time immemorial. Unlike your DVD player for your TV or your stereo CD player, the disc in your computer drive may be much more valuable than the drive itself. Yes, if you own the software legally, you should be able to get a replacement from the software company for a moderate charge, but maybe you need it now. In any case, the emergency release for the DVD tray doesn't require any special tools or skills, just a paperclip. Start by unbending a leg of the largest diameter paperclip that will fit in the hole on the faceplate of the drive. Next, insert it it straight into the hole, and if you're lucky, there will bee a little click before it goes in very far, and the tray will pop out a fraction of an inch. |
In the picture to the right, I haven't used any force at all, beyond gently pushing in the paperclip, and the CD tray popped out that far by itself. From here, it's an easy task to pull it out all the way so the disc can be removed. Below, I'm opening the DVD drive out of a Sony Vaio, but the tray didn't spring out when the paperclip pushed in the release, which you can tell by feel. So I had to pull on it with my fingernail behind the plastic facade while depressing the release. It opened pretty stiffly for the first fraction of an inch, and then pulled right out the rest of the way. That pretty much covers what you'll encounter with manually opening an optical drive, either it will pop open as soon as the paperclip works the latch, or you'll have to help it along. |
![]() |
![]() |
But there are instances in which the emergency release won't get the tray to eject. The worst of these is if a disc shattered at high speed and jammed all the mechanics up with little shards of plastic. You'll know this is the case by the noise if you gently tilt the drive back and forth. Another possibility is that an adhesive label peeled off in the drive and has gummed up the works. In either case, the odds of the drive being salvageable aren't very good, but if it was a label failure, you should be able to rescue the disc by disassembling the drive around it until the tray ejects or the disc is accessible. And before you rush out and buy a supposed generic replacement for the drive, remember that while the connector may be standard, the drive shell is customized, and you may not be able to transfer all of the shell hardware from one drive to another for mounting. |
When the paperclip trick works, it's one of the easiest laptop repairs you can do, and it's also pretty obvious when a stuck tray is the problem. But would youknow what to do if the tray opened and the laptop still wouldn't read DVD's? The Laptop Repair Workbook offers a two part approach to troubleshooting laptop hardware problems. We start by explaining the basic technologies and troubleshooting techniques, then we move on to advanced diagnostic flowcharts. The 191 page printable eBooks is available for instant download anywhere in the world, which beats getting it on CD in the mail! |
![]() |
Laptop Power Adapter and Supply - Illustrated how to repair laptop power cords
![]() |
One day your laptop may refuse to power on even though the AC adapter is plugged in. You've probably noticed that your laptop features an LED that lights up when live power is attached and the battery is charging, usually on the front of the laptop body. Older power adapters may also have a status LED to show they are functioning. The AC adapter may have failed if it's plugged into a good power outlet and the cable ends are securely seated in both the adapter and the laptop but power LED doesn't come on. Yet it's more likely the failure is the power lead from the adapter to the laptop. Your laptop may use a straight plug, like Toshiba and Lenovo, or an "L" connector like some Compaq and HP models, or a special proprietary design like some Dell and Sony adapter. The straight in power connectors probably have the highest failure rate because the cord often droops at a sharp angle. |
Try wiggling the cord a few inches back from the laptop jack and and see if the power LED on the laptop blinks. If the LED is unsteady or if it only lights if you position the cord a certain way, either the receptacle in the laptop or the wiring to the connector has failed. If you could choose, a bad cord is a much easier problem to repair, and that's what the illustrations on this page describe. Sometimes you won't see any sign of damage on a bad power cord no matter how closely you look because the insulation is unbroken. But the stranded wire inside the insulation could have frayed to the point that it only makes intermittent contact and melts open from current. The cable is normally shielded coax, with the inside conductor soldered to the inside of a barrel connector, and the coax shield soldered to the outside of the barrel connector. The solder joints are inside the molded plastic connector. | ![]() |
![]() |
The AC power cord that attaches the adapter to a wall outlet almost never fails as long as it's plugged in solidly. Laptop power cords usually include a ferrite choke to help prevent RF generated in the laptop from flowing back up the ground shield and turning it into a broadcast antenna. If it's too close to the molded connector to allow for replacement, I cut it off and hope nobody complains about interference. While you can always strip coaxial cable with a knife, it pays to own a decent wire stripper so you can make a clean job of it. I remove around 1" of the insulator from the braided shield and then twist the wires together off to one side. Classy technicians may tin the braid with a little solder before proceeding, but it's not really necessary if the connector has a tab with a hole. |
There's no point trying to reuse the original molded connector unless you are absolutely desperate, in which case you'll be stuck shaving away the plastic with a box cutter. I've had to do this while overseas when I couldn't find a replacement, but it was a bit of a mess since the ground braid was soldered directly to the outside barrel of the connector on the Toshiba I owned. And it can be tough to resolder manufactured connectors without melting everything because they aren't intended for multiple use. In the U.S. you can still find barrel connectors at Radio Shack, but bring along the original connector and the laptop to make sure you get the size right. You can often find the exact inner and outer diameter in millimeters (they're all metric) by searching on the Internet for AC adapter product descriptions for your laptop. | ![]() |
![]() |
Before you solder on the new connector, make sure you slide the plastic shell onto the cord in the proper orientation. It won't fit over the connector after the fact and you'll have to unsolder it all if you forget. If the shell doesn't fit onto the cord or your new connector doesn't include a shell, you can fake one up with many turns of electric tape. I generally leave enough room so the connector can fit into the laptop power jack as far as it will go, but good electrical contact is made before it's completely seated. In the picture I show the yellow inner conductor of the coax soldered to the tab that corresponds the center conductor of the barrel connector. The silver braid is soldered to the tab which corresponds to the outside of the barrel connector. You can use heat shrink tube over the tabs, if you have it, or even use a couple heat shrink layers in place of a shell. |
I tend not to trust the connector shell so I work a little electrical tape in between the two tabs to make sure they can't get crushed together and short. The trick is leaving enough room to get the shell over it all. The shell can be screwed onto connector since both pieces are threaded. After my first experience when I was forced to carve up a molded connector with a razor blade while travelling, I starting keeping a spare ready made in my laptop case. If the AC adapter cord I'm using fails, I can just cut off the end and splice on the replacement by twisting the wires together. The main failure mechanism for these cords is from the cord drooping down and flexing around when you work on your lap or run the laptop at the edge of a table. | ![]() |
![]() |
The problem shown on this page, a frayed or broken power adapter, is easy to diagnose. But most laptop issues benefit from careful troubleshooting before you rush to spend money on parts. The Laptop Repair Workbook is focused on troubleshooting laptop hardware. It includes an introductory section on all power and charging related problems, followed by an advanced flowchart for troubleshooting battery charging and AC power operation. The 191 page printable eBook version can be purchased for instant download anywhere in the world at about half the cost of buying the paperback and paying for shipping. |
Tuesday, August 28, 2012
IT MAN AKIWA MZIGONI KATIKA KUTAFUTA CHOCHOTE KITU
Hapo pia alikuwa kwa class akiwapigisha pindi vijana wake ktk chuo cha RUAHAA UNIVESITY COLLEGE.,Chuo hiko kiko ktk mkoa wa Iringa katikati ya mji
Monday, August 27, 2012
KIJANA CHIPUKIZI KTK ULIMWENGU WA TECHNOLOGY
Huyu ndiye kijana chipukizi, katika ulimwengu huu wa technology kwa xaxa makazi yake ni dar es salaam ,Sinza ukitaka kumpata kwa haraka zaidi utampata kwa no 0689362431,0656783670 & 0769309287www.facebook.comwww.twetter.comwww.tagged.com
Subscribe to:
Posts (Atom)